在鋼廠混合氣體循環(huán)發(fā)電工程中,控制閥需要控制混合氣體輸送管道中的壓力脈動(dòng),以確保輸送給氣體輪機(jī)的混合氣體壓力穩(wěn)定,機(jī)組正常發(fā)電?;旌蠚怏w的熱值較低,因此在相同的裝機(jī)容量下,混合氣體燃料管道的直徑和燃料控制閥的尺寸增加了3~4倍,相應(yīng)的混合氣體壓力控制閥的直徑也應(yīng)增加。增加閥門直徑是滿足大流量要求的有效措施之一。但控制閥部件尺寸的增加會(huì)使氣體密封性能更差。
混合氣體的主要可燃成分中含有有毒物質(zhì)CO氣體一旦泄漏,就會(huì)有安全隱患,因此研究大流量氣體燃料控制閥泄漏故障的診斷方法具有重要的現(xiàn)實(shí)意義。
1 控制閥泄漏故障機(jī)理
1.1 控制閥泄漏的類型
控制閥泄漏分為外部泄漏和內(nèi)部泄漏兩種類型。外部泄漏常見于閥體、閥桿、填料函和閥體之間的連接部調(diào)節(jié)閥關(guān)閉不嚴(yán)格形成的泄漏為內(nèi)部泄漏,發(fā)生在閥座密封處。以圖1所示結(jié)構(gòu)的控制閥為研究對(duì)象,重點(diǎn)研究其外部泄漏故障的機(jī)制。根據(jù)泄漏部位的不同,外部泄漏故障可分為:法蘭泄漏、閥蓋泄漏、壓力蓋泄漏、閥體泄漏。根據(jù)故障所涉及的不同部件,總結(jié)分析外部泄漏故障的分類,可獲得控制閥外部泄漏的機(jī)制。具體情況見表1。
1.2 泄漏時(shí)壓力變化
從混合氣體粘度的角度來看,當(dāng)流體沿管道流動(dòng)時(shí),由于流體分子及其與管壁之間的摩擦,必須消耗部分機(jī)械能來克服摩擦阻力;由于流動(dòng)方向和速度的變化,流體會(huì)產(chǎn)生局部漩渦和沖擊,機(jī)械能損失會(huì)導(dǎo)致流體壓力下降。因此,當(dāng)控制閥泄漏時(shí),泄漏處的流體流動(dòng)會(huì)帶來新的機(jī)械能損失,新的機(jī)械能損失會(huì)導(dǎo)致新的壓力損失。
控制閥入口壓力為p,出口壓力為p1,pf為了克服摩擦造成的壓力損失,壓力降低到Δp1.泄漏時(shí),出口壓力為p2,此時(shí)的壓力降為Δp2.泄漏造成的壓力損失為pL,有以下關(guān)系類型:
由式(4)可以看出,當(dāng)發(fā)生泄漏時(shí),控制閥的出口壓力在同一開度下降低。
由于混合氣體在傳輸過程中存在壓力信號(hào)波動(dòng),僅通過簡(jiǎn)單的壓力變化分析很難檢測(cè)到調(diào)節(jié)閥的泄漏故障,因此需要在此基礎(chǔ)上找到更有效的解決方案。
2 控制閥泄漏故障的診斷方法
2.1 混合氣體的流動(dòng)狀態(tài)
在建立控制閥泄漏故障數(shù)學(xué)模型時(shí),需要明確混合煤氣在控制閥中的流動(dòng)狀態(tài)和類別,以明確有關(guān)的邊界條件。
在鋼廠循環(huán)發(fā)電過程中,混合氣由高爐氣和焦?fàn)t氣組成,常用高焦比為7∶3.混合煤氣的組元體積及相關(guān)數(shù)據(jù)(表2)由高爐煤氣和焦?fàn)t煤氣獲得。
混合氣體的絕緣指數(shù)為Kh,氣體常數(shù)為Rh(J/kg•K),當(dāng)?shù)匾羲贋閍h(m/s),馬赫數(shù)為Mh,則有:
式中
R——?dú)怏w常數(shù),R=8.314J/mol•K;
T——混合氣體的溫度取平均溫度T=548K;
V——混合氣體的流速取平均流速V=16.25m/s。
由式(5)~(8))~(8)聯(lián)立求解混合氣體Mh=0.0367,即Mh<0.3.在流動(dòng)過程中,由壓力變化引起的密度變化不到5%。此時(shí),氣體可視為不可壓縮流體。因此,混合氣體的氣體流動(dòng)可視為不可壓縮流體流動(dòng),即混合氣體的密度ρ為常數(shù)。
♂
2.2 壓力與速度和密度的關(guān)系
壓力與速度的關(guān)系可以從流體力學(xué)中的伯努利方程中獲得。理想的不可壓縮流體伯努利方程為:
式中
γ -重度,N/m3,即γ=ρg;
ρ -混合氣體密度,kg/m3;
g -重力加速,m/s2;
V -氣閥入口速度,m/s;
V1-正常情況下氣閥出口速度,m/s;
z,z1-流體距離基準(zhǔn)在不同截面的高度,m。
考慮到實(shí)際摩擦力的影響和氣體重量較小的因素,公式(9)可以在實(shí)際控制閥的入口和出口推出伯努利方程,以獲得壓力和速度之間的關(guān)系:
密度與壓力之間的關(guān)系可根據(jù)氣體狀態(tài)方程獲得:
2.3 控制閥泄漏故障的數(shù)學(xué)模型
設(shè)Qm是閥體入口處的質(zhì)量流,即單位時(shí)間流入的質(zhì)量;Qm一是閥體出口處的質(zhì)量流;Qm2.泄漏時(shí)閥體出口處的質(zhì)量流。根據(jù)質(zhì)量守恒定律,如果沒有泄漏故障,流入控制閥的氣體質(zhì)量等于流出控制閥的氣體質(zhì)量,反之亦然。泄漏故障的數(shù)學(xué)模型為:
式中
V2-發(fā)生泄漏故障時(shí),混合氣體出口速度,m/s;
A——流過的斷面面積,m2。
將式(10)和(11)替代式(12)可獲得質(zhì)量流與壓力和流量之間的函數(shù)關(guān)系:
式中
Qv——?dú)忾y入口體積流量,m/s。
通過測(cè)量壓力和流量信號(hào),監(jiān)測(cè)質(zhì)量流量變化,診斷控制閥泄漏故障。
3 模擬和實(shí)現(xiàn)泄漏故障診斷
模擬根據(jù)質(zhì)量流變化建立的泄漏故障數(shù)學(xué)模型,模擬條件根據(jù)實(shí)際工藝條件確定:
a.入口壓力p在2.08~2.86MPa波動(dòng);
b.入口流量Qv在23.75~26.75m3/s波動(dòng);
c.?dāng)嗝婷娣eA=1.5384m2;
d混合氣體常數(shù)Rh=343.82J/kg•K;
e混合氣體溫度T=548K。
在LabVIEW在環(huán)境中,上述條件分別模擬控制閥的正常和泄漏狀態(tài)。模擬結(jié)果表明,當(dāng)泄漏故障發(fā)生時(shí),出口質(zhì)量流相對(duì)正常狀態(tài)的質(zhì)量流發(fā)生顯著變化,如圖2所示。
泄漏故障診斷部分作為控制閥智能故障診斷系統(tǒng)的子系統(tǒng),如圖3所示。
4 結(jié)束語
泄漏故障診斷是控制閥智能診斷系統(tǒng)的關(guān)鍵組成部分,泄漏故障信號(hào)的收集和處理對(duì)實(shí)現(xiàn)泄漏故障的自診斷具有重要意義。根據(jù)質(zhì)量守恒定律,比較控制閥出口和入口的質(zhì)量流變化,獲得以壓力信號(hào)和流量信號(hào)表達(dá)的質(zhì)量流量征兆作為故障診斷征兆的具體解決方案,通過模擬實(shí)驗(yàn)證明了診斷方法的有效性。
咨詢需求
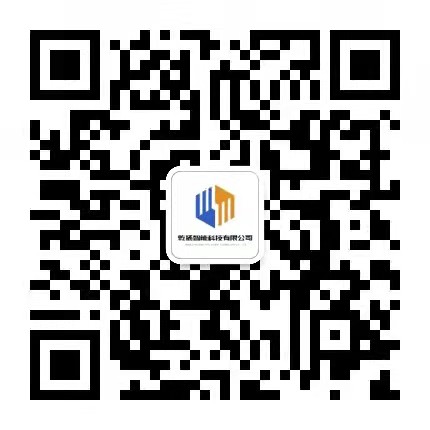